Total control from the beginning to the end.
INTEGRAL TRACEABILITY SYSTEM
We have an agricultural production area that exceeds 20,000 hectares between owned and rented fields; all managed according to the Integral Traceability System that keeps the complete history of each stage and allows the tracking of peanuts from sowing to the final consumer.
The lots are sequentially processed, and with each new lot that enters the process, a complete cleaning is carried out to avoid mixtures.
Each product delivered complies with the following identification:
- Seeds (type, reproductive generation)
- Soil and planting (soil quality and conditioning, sowing and harvesting calendar))
- Process (yield by granulometry)
- Quality throughout the process (physical and chemical analysis)
- Quality certificates for export, carried out by independent entities, such as SGS and JLA, duly supervised by Argentine authorities (SENASA); phytosanitary and laboratory certificates, weight and count control, quality and conditioning, aflatoxins, fumigation, cleaning and conditioning of containers, etc.
Our processes
WORK IN THE FIELD
The peanut sowing and harvesting cycle runs from October to May.
It all begins with sowing, when specialized professionals carefully choose the most suitable land for cultivation, guaranteeing the production of ripe and healthy grains.
Soil preparation is determined according to the needs of each lot, we always try not to exceed the tillage in order not to affect its stability and prevent water and wind erosion. Once the grains have reached ripening, the plants are uprooted. This task is carried out with special care, since it will have an essential influence on the final quality of the peanuts.
The last task carried out in the field is the harvesting of the pods. State-of-the-art harvesters allow the pods to be harvested with minimal losses; therefore, perfectly preserving their quality.
Then, the industrial process begins.
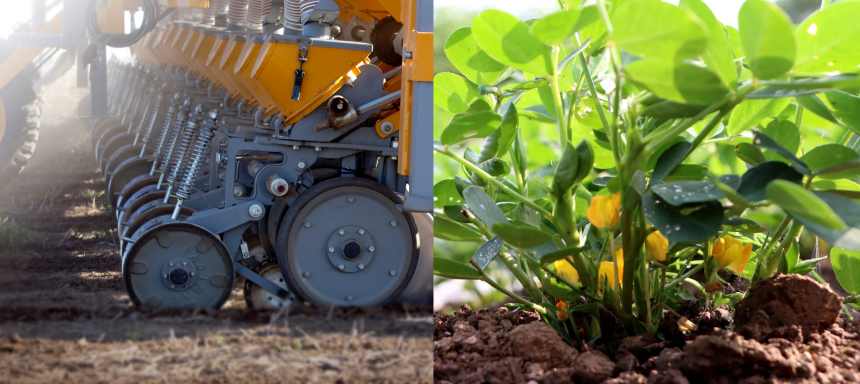
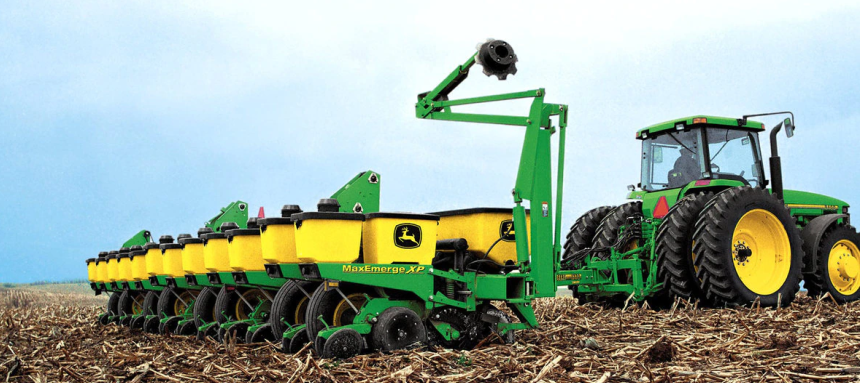
Our technology
We have a processing plant equipped with the latest technology in peanut selection available in the market, and highly trained labor force for this purpose.
Continuous research and innovation in the different stages of production support the work of our qualified personnel, involved in the objective of obtaining the best product and fulfill our customers' needs.
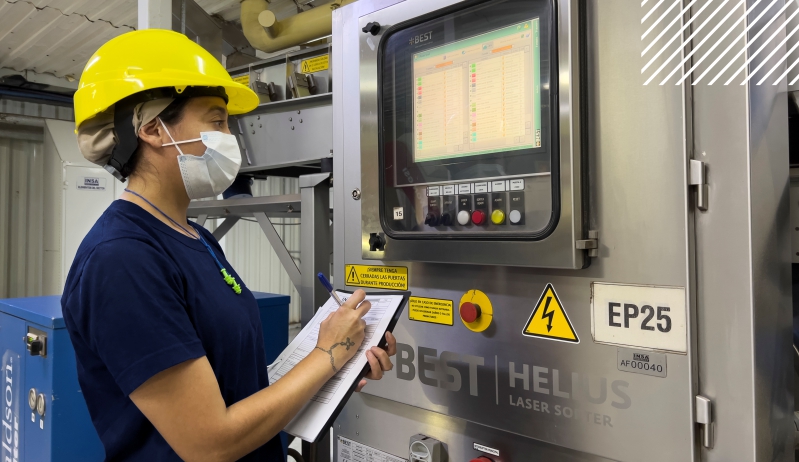
State-of-the-art facilities.
The plant has a refrigerated warehouse of 8,000 tons for finished products that meets the optimal conditions of temperature, humidity and sanitation necessary to store peanuts, maintaining their quality for a longer period.
WE HAVE CONDITIONING AND STORAGE CONTAINERS FOR RAW MATERIAL OF APPROXIMATELY 28,000 TONS AND A PROCESSING CAPACITY OF 200 TONS PER DAY OF CONFECTIONERY PEANUTS SUITABLE FOR EXPORT.